Comprehensive Overview: What is Porosity in Welding and How to stop It
The Science Behind Porosity: A Comprehensive Guide for Welders and Fabricators
Recognizing the complex mechanisms behind porosity in welding is vital for welders and makers making every effort for impeccable craftsmanship. From the composition of the base materials to the details of the welding process itself, a multitude of variables conspire to either aggravate or relieve the visibility of porosity.
Comprehending Porosity in Welding
FIRST SENTENCE:
Evaluation of porosity in welding discloses important understandings into the stability and top quality of the weld joint. Porosity, defined by the visibility of cavities or voids within the weld metal, is a common issue in welding processes. These voids, otherwise effectively attended to, can compromise the architectural honesty and mechanical buildings of the weld, bring about possible failings in the ended up item.
To detect and evaluate porosity, non-destructive screening techniques such as ultrasonic screening or X-ray examination are typically utilized. These methods permit the recognition of internal issues without endangering the honesty of the weld. By assessing the dimension, form, and circulation of porosity within a weld, welders can make enlightened choices to improve their welding processes and accomplish sounder weld joints.

Elements Affecting Porosity Formation
The incident of porosity in welding is affected by a myriad of variables, ranging from gas securing effectiveness to the ins and outs of welding specification setups. Welding parameters, consisting of voltage, existing, travel speed, and electrode kind, also influence porosity formation. The welding method employed, such as gas steel arc welding (GMAW) or shielded metal arc welding (SMAW), can influence porosity development due to variations in warmth distribution and gas protection - What is Porosity.
Effects of Porosity on Weld High Quality
Porosity development considerably jeopardizes the structural stability and mechanical residential or commercial properties of bonded joints. When porosity exists in a weld, it produces gaps or cavities within the material, minimizing the overall strength of the joint. These spaces work as stress concentration points, making the weld extra susceptible to breaking and failure under tons. The visibility of porosity also weakens the weld's resistance to deterioration, as the entraped air or gases within the voids can respond with the surrounding environment, causing destruction over time. Additionally, porosity can impede the weld's capacity to endure pressure or influence, more endangering the total top quality and dependability of the bonded structure. In vital applications such as aerospace, auto, or structural constructions, where safety and security and resilience are critical, the damaging impacts of porosity on weld quality can have serious consequences, emphasizing the significance of decreasing porosity through correct welding methods and treatments.
Techniques to Decrease Porosity
Furthermore, making use of the ideal welding parameters, such as the appropriate voltage, present, and take a trip rate, is essential in stopping porosity. Keeping a regular arc size and angle throughout welding also helps decrease the probability of porosity.

Using the ideal welding method, such as back-stepping or employing a weaving motion, can additionally assist distribute warmth uniformly and decrease the chances of porosity development. By executing these techniques, welders can properly click resources reduce porosity and produce high-quality bonded joints.
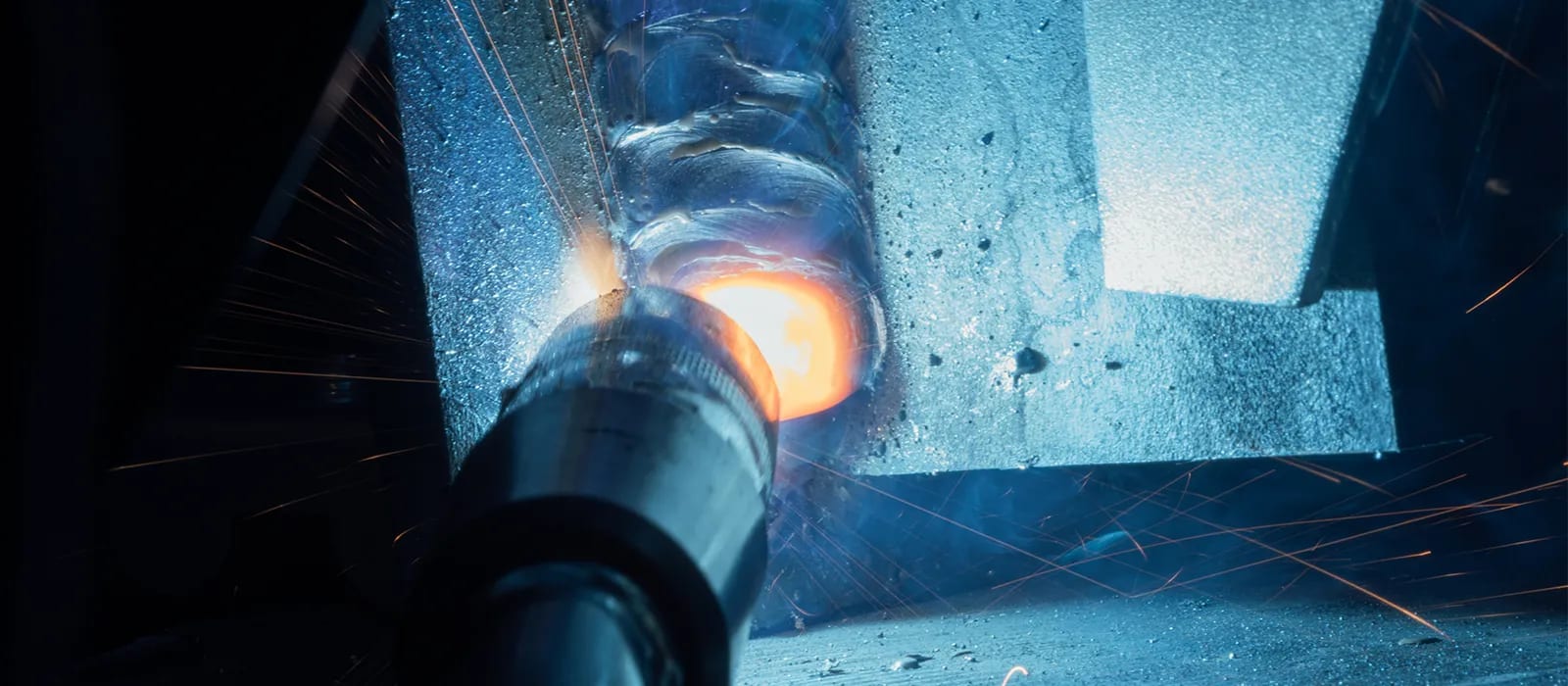
Advanced Solutions for Porosity Control
Applying cutting-edge modern technologies and ingenious techniques plays a pivotal duty in accomplishing superior control over porosity in welding processes. One innovative option is using advanced gas combinations. Protecting gases like helium or a mixture of argon and hydrogen can help in reducing porosity by supplying better arc security and improved gas protection. Additionally, utilizing innovative welding methods such as pulsed MIG welding or modified environment welding can also assist minimize porosity problems.
An additional innovative solution includes the usage of see this page advanced welding tools. Making use of tools with integrated features like waveform control and sophisticated power sources can improve weld top quality and reduce porosity threats. The execution of automated welding systems with exact control over criteria can considerably lessen porosity issues.
In look at this now addition, incorporating innovative monitoring and inspection technologies such as real-time X-ray imaging or automated ultrasonic screening can assist in spotting porosity early in the welding process, permitting immediate rehabilitative activities. Generally, integrating these sophisticated services can significantly improve porosity control and enhance the total high quality of welded components.
Verdict
In verdict, recognizing the science behind porosity in welding is vital for welders and producers to produce high-quality welds. By identifying the factors affecting porosity formation and implementing strategies to reduce it, welders can improve the total weld high quality. Advanced services for porosity control can further improve the welding procedure and guarantee a solid and trusted weld. It is essential for welders to constantly educate themselves on porosity and apply finest practices to accomplish optimal results.